Examine This Report on Alcast Company
Examine This Report on Alcast Company
Blog Article
The 5-Second Trick For Alcast Company
Table of ContentsExamine This Report about Alcast CompanyAlcast Company Can Be Fun For AnyoneGetting The Alcast Company To WorkThe Single Strategy To Use For Alcast Company7 Easy Facts About Alcast Company ShownThe 8-Minute Rule for Alcast Company
Chemical Comparison of Cast Aluminum Alloys Silicon promotes castability by reducing the alloy's melting temperature level and boosting fluidness during spreading. Furthermore, silicon adds to the alloy's strength and use resistance, making it important in applications where longevity is important, such as vehicle components and engine parts.It likewise enhances the machinability of the alloy, making it less complicated to process into finished products. In this way, iron contributes to the total workability of light weight aluminum alloys.
Manganese adds to the stamina of aluminum alloys and enhances workability (Aluminum Casting). It is generally utilized in functioned light weight aluminum items like sheets, extrusions, and accounts. The presence of manganese aids in the alloy's formability and resistance to splitting during manufacture processes. Magnesium is a lightweight component that gives strength and effect resistance to aluminum alloys.
8 Simple Techniques For Alcast Company
It permits the manufacturing of light-weight parts with outstanding mechanical residential or commercial properties. Zinc boosts the castability of aluminum alloys and assists control the solidification process throughout casting. It boosts the alloy's toughness and hardness. It is usually located in applications where complex forms and fine information are necessary, such as ornamental spreadings and specific vehicle parts.
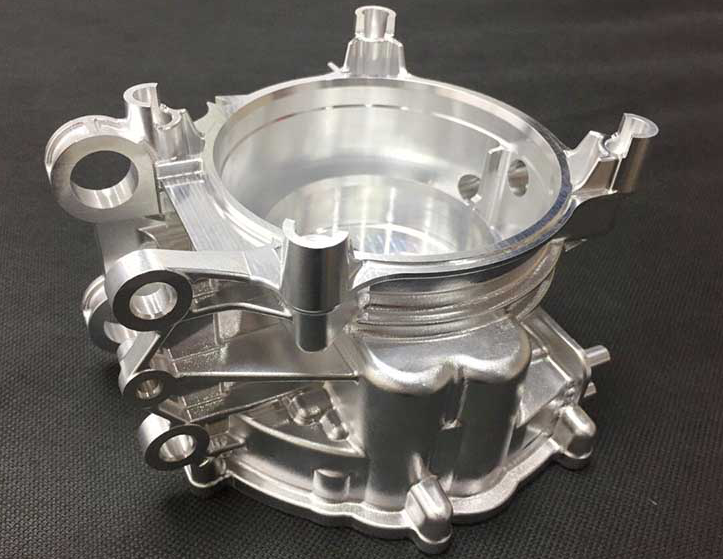
The key thermal conductivity, tensile strength, yield toughness, and elongation differ. Select suitable resources according to the efficiency of the target item produced. Amongst the above alloys, A356 has the highest possible thermal conductivity, and A380 and ADC12 have the least expensive. The tensile limitation is the opposite. A360 has the best return strength and the highest possible elongation price.
The Definitive Guide for Alcast Company
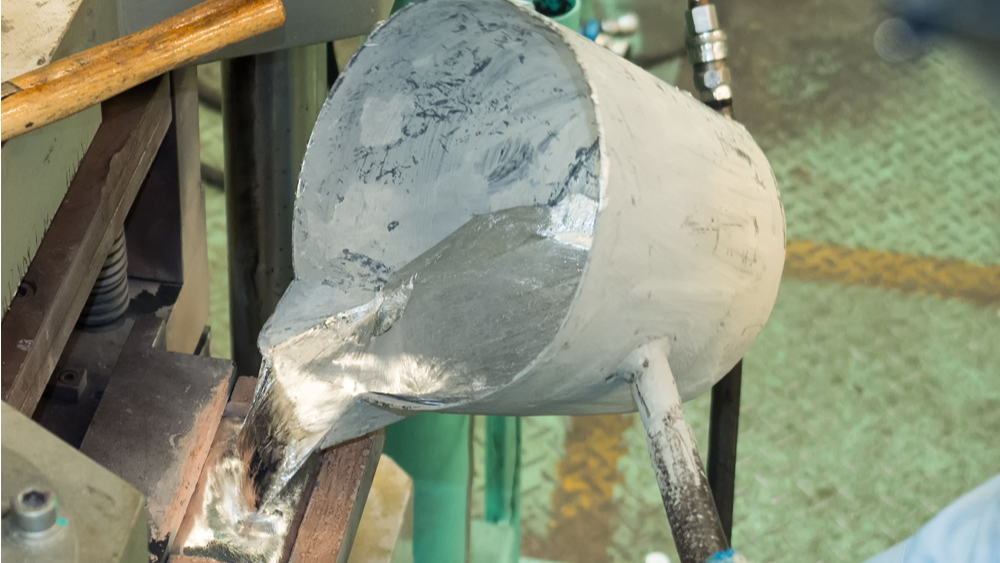
In accuracy casting, 6063 is appropriate for applications where intricate geometries and high-quality surface area finishes are paramount. Examples consist of telecommunication rooms, where the alloy's premium formability enables sleek and visually pleasing styles while keeping structural honesty. In the Lights Solutions industry, precision-cast 6063 parts produce elegant and reliable illumination components that require complex forms and great thermal performance.
The A360 shows remarkable prolongation, making it excellent for complex and thin-walled elements. In accuracy casting applications, A360 is well-suited for sectors such as Consumer Electronics, Telecommunication, and Power Devices.
Rumored Buzz on Alcast Company
Its unique residential or commercial properties make A360 a useful selection for accuracy casting in these sectors, enhancing product sturdiness and top quality. Aluminum alloy 380, or A380, is a commonly used casting alloy with several distinctive characteristics. It supplies outstanding castability, making it a suitable option for accuracy spreading. A380 displays excellent fluidness when molten, guaranteeing intricate and in-depth molds are accurately duplicated.
In accuracy spreading, light weight aluminum 413 beams in the Consumer Electronic Devices and Power Equipment industries. This alloy's remarkable rust resistance makes it a superb option for outside applications, guaranteeing durable, sturdy items in the mentioned sectors.
Things about Alcast Company
The aluminum alloy you select will significantly impact both the spreading process and the properties of the last item. Because of this, you have to make your decision carefully and take an informed technique.
Figuring out the most ideal aluminum alloy for your application will imply weighing a wide array of qualities. The initial classification addresses alloy characteristics that affect the manufacturing process.
The smart Trick of Alcast Company That Nobody is Talking About
The alloy you select for die casting straight affects a number of facets of the spreading process, like just how simple the alloy is to function with and if it is vulnerable to casting defects. Warm fracturing, likewise called solidification cracking, is a normal die casting issue for light weight aluminum alloys that can lead to inner or surface-level tears or fractures.
Certain light weight aluminum alloys are much more susceptible to hot splitting than others, and your choice should consider this. An additional usual issue discovered in the die casting of light weight aluminum is pass away soldering, which is when the actors stays with the die walls and makes ejection difficult. It can additional info damage both the cast and the die, so you ought to try to find alloys with high anti-soldering residential or commercial properties.
Corrosion resistance, which is already a remarkable characteristic of light weight aluminum, can differ considerably from alloy to alloy and is a crucial characteristic to think about depending upon the environmental problems your item will certainly be revealed to (Casting Foundry). Use resistance is an additional residential property generally sought in aluminum products and can differentiate some alloys
Report this page